From human organs to houses, the decreased cost and increased attention to three-dimensional, or 3D, printing is putting these machines in the hands of several industries that are eager to try them out and make prototypes.
NASA is experimenting with 3D printers by taking them to the final frontier. Testing a 3D printer on the International Space Station was the first step towards establishing an on-demand machine shop in space. Three-dimensional printing offers a fast and inexpensive way to manufacture parts on-site and on-demand, a huge benefit to long-term missions with restrictions on weight and room for cargo.
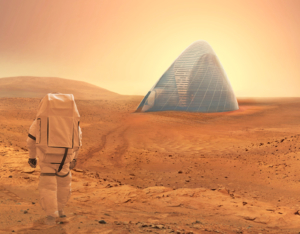
Mars Ice House NASA Habitat Challenge
NASA just completed phase 2 of their $2.5 million 3D-Printed Habitat Challenge, an architectural competition to design a colony in space. The goal is to not transport materials from Earth, but use what the planet has to offer for construction. Phase 3, which is currently under development, will focus on fabrication of complete habitats and will debut in August. View more on an out of this world challenge.
When astronauts head to Mars, they will need a safe place to stay on a planet with an atmosphere that doesn’t provide protection from high-energy radiation. For researchers at NASA’s Langley Research Center in Hampton, Va., the best building material for a new home on Mars may lie in an unexpected material: ice. Nasa experts, designers and architects came up with a Mars Ice Dome.
In May, engineers from a U.S. commercial space firm successfully launched a 3D rocket from New Zealand into space, but not into orbit. The carbon-composite rocket, whose engine took a full 24 hours to print, made it up past Earth’s atmosphere with a cargo of sensors. Data will now be analyzed to figure out how to improve the rocket, named the Electron.
The technique of 3D printing is spreading rapidly in the field of medicine. Many hearing aids and dental crowns are now 3D-printed, as are disposable surgical instruments and even prosthetic limbs. In 2014, the federally funded National Institute of Health launched the NIH 3D Print Exchange, a public website that enables users to share, download and edit 3D print files related to health and science.
Perhaps, in the future, patients won’t have to wait on a donor list for an organ transplant. The 3D bioprinter is used to fabricate functional human tissues that possess human tissue-like composition and architecture. Those functional tissues can be used for repairing damaged tissues and regeneration. Bioprinting is like regular inkjet printing, but the bioprinters use living cells instead of pigment-based inks and inject the cells into a matrix instead of printing on paper.
Scientists have already been able to successfully print lung tissues. The process includes printing a cluster of basic lung epithelial tissues which are then allowed to grow and proliferate, becoming the trachea. Drugs are injected into this system to make the artificial trachea contract and expand much like our normal wind pipe would do.
Using a 3D printer to build us a place to live and work on our current planet has been happening for a few years. In 2015, It took 17 days for a 3D printer to print a 2,700-square-foot office building in Dubai, United Arab Emirates. In 2015, China successfully 3D-printed a five-story apartment building and a three-story mansion that were constructed using a 500-foot-long 3D printer. The villa cost about $161,000 to build, decreased production time between 50 and 70 percent and saved between 30 and 60 percent of construction waste.
A San Francisco-based 3D-printing startup, recently showed it can 3D-print concrete walls for a small house in less than 24 hours. Using a 3D printer to lay down concrete walls on a test site in Russia, the firm was able to print a 400-square-foot house. The printer, which resembles a small crane, places layers of a concrete mixture the company claims can last for 175 years and after the walls have been laid, the printer is removed and insulation, windows, appliances and a roof is added. Advocates of 3D printed-structures tout that they are affordable with less waste, can resist winds of up to 220 mph, use of natural materials, compatibility with Internet of Things devices and lower insurance costs because the materials carry low-risk hazards such as fire and roof damage.
SPI’s e-newsletters are an excellent source of government contracting opportunities. Sign up today to ensure you never miss out!